Professional Manufacturer Of Hydraulic Metal Cutting Band Saw Machines
Committed to becoming a well-known manufacturer of hydraulic metal cutting band saw machines.

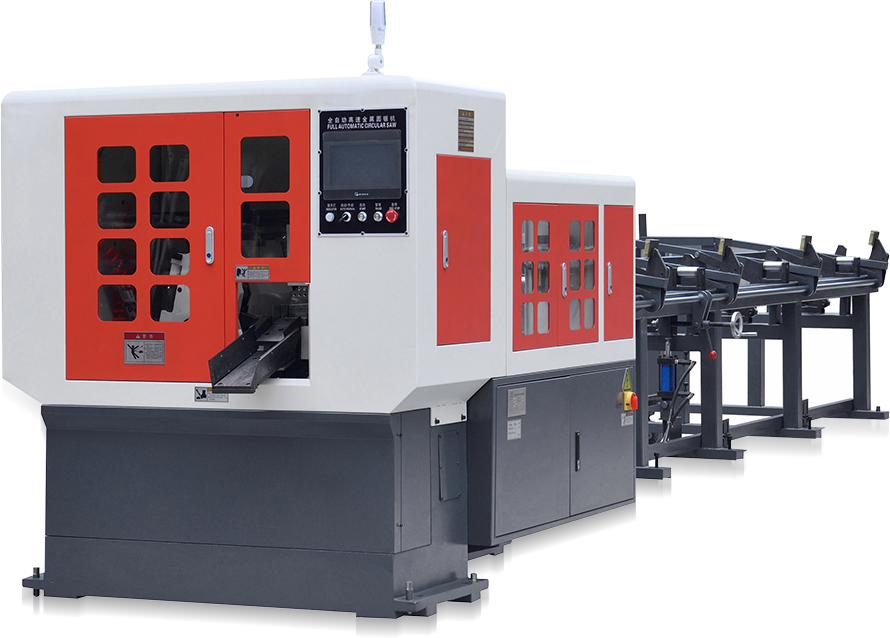
Advanced technical strength and effective technical guarantee.
Flexible business philosophy and professional services.
Advanced manufacturing technology, strictly controlled product quality and good reputation.
For any questions and feedback from customers, we will reply patiently and meticulously.
Pay Attention To Our Latest News And Exhibitions.
Metal Cutting Bandsaw Machines play a vital role in many industrial processes. These machines provide efficient and precise cutting solutions for a variety of metals. Our company specializes in producing metal cutting bandsaw machines and vertical metal bandsaw machines to meet the needs of different customers at home and abroad. Understanding the characteristics and practical applications of these machines can help users choose the right equipment and improve their workflow. Main Features of Metal Cutting Bandsaw Machines Metal cutting bandsaw machines are designed to process various types and thicknesses of metal. Its cutting blade consists of a continuous metal strip with sharp teeth that can smoothly cut through the material. This method reduces waste and provides precise cutting, which is essential for manufacturing and processing. One of the advantages of these machines is their ability to efficiently process large and small workpieces. Adjustable cutting speed and blade tension control allow operators to adjust the performance of the machine according to the material being cut. This flexibility helps reduce saw blade wear and maintain cutting accuracy over time. These machines also focus on safety and user convenience. Features such as automatic shutdown, protective covers, and ergonomic controls reduce the risk of accidents and improve ease of use. Regular maintenance of blades and components ensures consistent performance and extends the life of your machine. Advantages of Vertical Metal Bandsaws Vertical metal bandsaws differ from horizontal models in that their blades are placed vertically, allowing for different cutting styles. This design is particularly useful for cutting longer, heavier metal pieces. The vertical design allows for a more visible cut line, allowing for more precise positioning and calibration. These machines are often equipped with hydraulic or mechanical clamps to firmly clamp the material during the cutting process, reducing vibration and improving cut quality. Vertical bandsaws are widely used in metal fabrication shops, construction sites, and manufacturing plants because of their adaptability and reliability. Adjustability is another important aspect. Operators can easily set cutting angles and speeds to accommodate complex shapes and materials, thereby increasing production efficiency. The vertical placement also saves floor space, making these machines ideal for workshops with limited space. Choose the bandsaw that suits your needs Whether to choose a metal cutting bandsaw or a vertical metal bandsaw depends on the specific job requirements. Horizontal bandsaws are generally suitable for regular straight-line cuts and large-scale production, while vertical bandsaws are better suited for special cuts and irregular shapes. Considering factors such as material type, thickness, production volume, and available workspace can help guide decisions. It is also helpful to evaluate machine features such as blade size compatibility, motor power, and control systems to ensure they align with operational goals. Working closely with suppliers can provide insight into the appropriate machine configuration for each application. Understanding warranty terms, maintenance support, and the availability of replacement parts can help make a wise investment. Maintaining Bandsaws to Ensure Consistent Performance Routine maintenance is essential to maintaining cutting accuracy and machine durability. Regularly checking blade condition, adjusting tension, and lubricating moving parts can help prevent breakdowns. Cleaning debris from the machine and ensuring all safety devices are functioning properly can ensure a safe working environment. Training operators to properly use and maintain machines can reduce errors and extend the life of the equipment. Keeping detailed maintenance logs can help track machine health and schedule timely repairs or part replacements. By following these practices, companies can downtime and maintain a stable production schedule while ensuring consistent product quality. Applications and Industry Use Metal cutting band sawing machines find applications in various industries, including automotive, construction, shipbuilding, and machinery manufacturing. Their ability to handle diverse materials such as steel, aluminum, and brass makes them versatile tools for many fabrication needs. Vertical metal band saws are especially useful when dealing with large structural components, pipes, and profiles. Their precision and adaptability support complex manufacturing processes that demand reliable cutting accuracy. Whether producing parts for mass production or custom fabrication, these machines contribute to efficient workflows and resource savings.
Metal Cutting Bandsaw Machines play a vital role in many industrial processes. These machines provide efficient and precise cutting solutions for a variety of metals. Our company specializes in producing metal cutting bandsaw machines and vertical metal bandsaw machines to meet the needs of different customers at home and abroad. Understanding the characteristics and practical applications of these machines can help users choose the right equipment and improve their workflow. Main Features of Metal Cutting Bandsaw Machines Metal cutting bandsaw machines are designed to process various types and thicknesses of metal. Its cutting blade consists of a continuous metal strip with sharp teeth that can smoothly cut through the material. This method reduces waste and provides precise cutting, which is essential for manufacturing and processing. One of the advantages of these machines is their ability to efficiently process large and small workpieces. Adjustable cutting speed and blade tension control allow operators to adjust the performance of the machine according to the material being cut. This flexibility helps reduce saw blade wear and maintain cutting accuracy over time. These machines also focus on safety and user convenience. Features such as automatic shutdown, protective covers, and ergonomic controls reduce the risk of accidents and improve ease of use. Regular maintenance of blades and components ensures consistent performance and extends the life of your machine. Advantages of Vertical Metal Bandsaws Vertical metal bandsaws differ from horizontal models in that their blades are placed vertically, allowing for different cutting styles. This design is particularly useful for cutting longer, heavier metal pieces. The vertical design allows for a more visible cut line, allowing for more precise positioning and calibration. These machines are often equipped with hydraulic or mechanical clamps to firmly clamp the material during the cutting process, reducing vibration and improving cut quality. Vertical bandsaws are widely used in metal fabrication shops, construction sites, and manufacturing plants because of their adaptability and reliability. Adjustability is another important aspect. Operators can easily set cutting angles and speeds to accommodate complex shapes and materials, thereby increasing production efficiency. The vertical placement also saves floor space, making these machines ideal for workshops with limited space. Choose the bandsaw that suits your needs Whether to choose a metal cutting bandsaw or a vertical metal bandsaw depends on the specific job requirements. Horizontal bandsaws are generally suitable for regular straight-line cuts and large-scale production, while vertical bandsaws are better suited for special cuts and irregular shapes. Considering factors such as material type, thickness, production volume, and available workspace can help guide decisions. It is also helpful to evaluate machine features such as blade size compatibility, motor power, and control systems to ensure they align with operational goals. Working closely with suppliers can provide insight into the appropriate machine configuration for each application. Understanding warranty terms, maintenance support, and the availability of replacement parts can help make a wise investment. Maintaining Bandsaws to Ensure Consistent Performance Routine maintenance is essential to maintaining cutting accuracy and machine durability. Regularly checking blade condition, adjusting tension, and lubricating moving parts can help prevent breakdowns. Cleaning debris from the machine and ensuring all safety devices are functioning properly can ensure a safe working environment. Training operators to properly use and maintain machines can reduce errors and extend the life of the equipment. Keeping detailed maintenance logs can help track machine health and schedule timely repairs or part replacements. By following these practices, companies can downtime and maintain a stable production schedule while ensuring consistent product quality. Applications and Industry Use Metal cutting band sawing machines find applications in various industries, including automotive, construction, shipbuilding, and machinery manufacturing. Their ability to handle diverse materials such as steel, aluminum, and brass makes them versatile tools for many fabrication needs. Vertical metal band saws are especially useful when dealing with large structural components, pipes, and profiles. Their precision and adaptability support complex manufacturing processes that demand reliable cutting accuracy. Whether producing parts for mass production or custom fabrication, these machines contribute to efficient workflows and resource savings.
Vertical metal band sawing machines have become an essential part of fabrication workshops and manufacturing plants that require efficient cutting solutions for a broad range of metal profiles. As production demands grow and materials diversify, selecting the appropriate vertical band saw and understanding its operation are increasingly important for companies aiming to balance throughput, precision, and cost management. Key Advantages of Vertical Metal Band Saws Unlike horizontal band saws, vertical configurations offer distinctive benefits when cutting complex shapes or managing long, irregular workpieces. A vertical metal band sawing machine positions the blade perpendicular to the work table, allowing operators to maneuver parts manually or with auxiliary supports. This flexibility is particularly useful in heavy-duty fabrication environments where workpieces vary in size and geometry. Vertical band saws can accommodate straight cuts, contour cuts, and miter cuts without requiring major adjustments. For fabricators handling custom orders or limited production batches, this adaptability helps reduce setup time and material handling challenges. Because the workpiece is usually guided by hand or with a mechanical feeder, it is easier to achieve cuts that follow marked outlines or templates. These characteristics make vertical band saws an important complement to horizontal machines, which are better suited to repetitive straight cuts. In operations where versatility is a priority, vertical models often occupy a central role. Typical Applications in Fabrication and Maintenance Vertical band sawing machines are used across a wide spectrum of industries, including structural steel fabrication, pressure vessel production, and equipment repair. They are particularly valued in job shops where operators must quickly switch between different materials such as mild steel, stainless alloys, aluminum, and tool steel. One of the common applications involves trimming excess material from large welded assemblies or plate structures before machining. By using a vertical saw for preliminary cuts, operators can remove surplus sections more efficiently than with oxy-fuel or plasma methods. This approach often results in smoother edges and reduces the need for secondary grinding. Another frequent use is preparing metal blanks for further processing. Vertical band saws can cut round, square, and irregular stock into approximate dimensions, supporting CNC machining or manual fabrication downstream. In maintenance departments, these machines help create replacement parts or modify existing components with shorter processing times. Features to Evaluate When Selecting a Vertical Band Saw There are several technical specifications and operating factors to consider when purchasing a vertical metal band saw. The throat capacity (the distance between the saw blade and the upright) affects the width of material the saw can handle. For heavy-duty fabrication, a larger throat size provides more flexibility, especially when cutting large panels or frames. Blade speed control is another important factor. Variable speed drives allow operators to adjust blade movement to match the hardness and thickness of different metals. Slower speeds are often needed for harder alloys to reduce heat generation and extend blade life. Conversely, higher speeds can improve productivity when working with softer materials. Blade guides and tension systems also influence cut quality and machine longevity. Precision guides help maintain accurate tracking, while consistent tension reduces the risk of blade slippage or premature wear. Many modern models include hydraulic tensioning mechanisms that simplify adjustment and improve repeatability. For workshops planning to handle large volumes or heavy components, additional features such as integrated material support tables, chip conveyors, and coolant systems can improve efficiency and extend tool life. Operating Practices for Consistent Performance Achieving predictable results with a vertical band saw requires consistent operating practices and routine maintenance. Before each shift, operators should verify that the blade is properly tensioned and free of damage. Worn or chipped teeth can cause wandering cuts or excessive vibration, which may compromise part accuracy and shorten blade life. During operation, applying appropriate feed pressure helps avoid overloading the blade. Excessive force can generate heat and accelerate wear, while insufficient pressure may result in poor cutting performance. Most machines are designed to support steady, moderate feeding that balances productivity and tool preservation. Coolant use also contributes to cut quality. Properly applied coolant reduces friction, cools the blade, and clears chips from the kerf. Many heavy-duty models are equipped with recirculating coolant systems that maintain a continuous flow, reducing manual intervention and improving surface finish. Periodic cleaning and inspection are essential to maintain reliable operation. Chips and debris should be cleared from the work table and drive mechanisms. Lubrication of bearings and guides helps prevent premature wear. Operators should also check drive belts and hydraulic systems to ensure they are functioning as intended. Incorporating Vertical Bandsaws Into Fabrication Workflows Integrating vertical metal band sawing machines alongside other equipment can streamline material preparation and improve overall workflow. In many fabrication shops, vertical saws are positioned near incoming material storage so that raw stock can be cut to manageable sizes before moving to welding stations or machining centers. Combining vertical saws with metal cutting band sawing machines allows companies to assign tasks based on the complexity and quantity of cuts. For example, a horizontal band saw might handle repeated straight sections of tubing or bar stock, while the vertical saw is reserved for contour cuts, slotting, and custom trimming. This division of labor can increase throughput without requiring major changes to layout or staffing. By selecting appropriate equipment, maintaining consistent practices, and training operators in safe and efficient use, fabrication businesses can leverage the strengths of vertical band sawing machines to meet varied production requirements. Whether used for structural components, maintenance work, or custom assemblies, these machines offer a practical combination of precision and versatility that supports high-quality results across diverse applications.
Vertical metal band sawing machines have become an essential part of fabrication workshops and manufacturing plants that require efficient cutting solutions for a broad range of metal profiles. As production demands grow and materials diversify, selecting the appropriate vertical band saw and understanding its operation are increasingly important for companies aiming to balance throughput, precision, and cost management. Key Advantages of Vertical Metal Band Saws Unlike horizontal band saws, vertical configurations offer distinctive benefits when cutting complex shapes or managing long, irregular workpieces. A vertical metal band sawing machine positions the blade perpendicular to the work table, allowing operators to maneuver parts manually or with auxiliary supports. This flexibility is particularly useful in heavy-duty fabrication environments where workpieces vary in size and geometry. Vertical band saws can accommodate straight cuts, contour cuts, and miter cuts without requiring major adjustments. For fabricators handling custom orders or limited production batches, this adaptability helps reduce setup time and material handling challenges. Because the workpiece is usually guided by hand or with a mechanical feeder, it is easier to achieve cuts that follow marked outlines or templates. These characteristics make vertical band saws an important complement to horizontal machines, which are better suited to repetitive straight cuts. In operations where versatility is a priority, vertical models often occupy a central role. Typical Applications in Fabrication and Maintenance Vertical band sawing machines are used across a wide spectrum of industries, including structural steel fabrication, pressure vessel production, and equipment repair. They are particularly valued in job shops where operators must quickly switch between different materials such as mild steel, stainless alloys, aluminum, and tool steel. One of the common applications involves trimming excess material from large welded assemblies or plate structures before machining. By using a vertical saw for preliminary cuts, operators can remove surplus sections more efficiently than with oxy-fuel or plasma methods. This approach often results in smoother edges and reduces the need for secondary grinding. Another frequent use is preparing metal blanks for further processing. Vertical band saws can cut round, square, and irregular stock into approximate dimensions, supporting CNC machining or manual fabrication downstream. In maintenance departments, these machines help create replacement parts or modify existing components with shorter processing times. Features to Evaluate When Selecting a Vertical Band Saw There are several technical specifications and operating factors to consider when purchasing a vertical metal band saw. The throat capacity (the distance between the saw blade and the upright) affects the width of material the saw can handle. For heavy-duty fabrication, a larger throat size provides more flexibility, especially when cutting large panels or frames. Blade speed control is another important factor. Variable speed drives allow operators to adjust blade movement to match the hardness and thickness of different metals. Slower speeds are often needed for harder alloys to reduce heat generation and extend blade life. Conversely, higher speeds can improve productivity when working with softer materials. Blade guides and tension systems also influence cut quality and machine longevity. Precision guides help maintain accurate tracking, while consistent tension reduces the risk of blade slippage or premature wear. Many modern models include hydraulic tensioning mechanisms that simplify adjustment and improve repeatability. For workshops planning to handle large volumes or heavy components, additional features such as integrated material support tables, chip conveyors, and coolant systems can improve efficiency and extend tool life. Operating Practices for Consistent Performance Achieving predictable results with a vertical band saw requires consistent operating practices and routine maintenance. Before each shift, operators should verify that the blade is properly tensioned and free of damage. Worn or chipped teeth can cause wandering cuts or excessive vibration, which may compromise part accuracy and shorten blade life. During operation, applying appropriate feed pressure helps avoid overloading the blade. Excessive force can generate heat and accelerate wear, while insufficient pressure may result in poor cutting performance. Most machines are designed to support steady, moderate feeding that balances productivity and tool preservation. Coolant use also contributes to cut quality. Properly applied coolant reduces friction, cools the blade, and clears chips from the kerf. Many heavy-duty models are equipped with recirculating coolant systems that maintain a continuous flow, reducing manual intervention and improving surface finish. Periodic cleaning and inspection are essential to maintain reliable operation. Chips and debris should be cleared from the work table and drive mechanisms. Lubrication of bearings and guides helps prevent premature wear. Operators should also check drive belts and hydraulic systems to ensure they are functioning as intended. Incorporating Vertical Bandsaws Into Fabrication Workflows Integrating vertical metal band sawing machines alongside other equipment can streamline material preparation and improve overall workflow. In many fabrication shops, vertical saws are positioned near incoming material storage so that raw stock can be cut to manageable sizes before moving to welding stations or machining centers. Combining vertical saws with metal cutting band sawing machines allows companies to assign tasks based on the complexity and quantity of cuts. For example, a horizontal band saw might handle repeated straight sections of tubing or bar stock, while the vertical saw is reserved for contour cuts, slotting, and custom trimming. This division of labor can increase throughput without requiring major changes to layout or staffing. By selecting appropriate equipment, maintaining consistent practices, and training operators in safe and efficient use, fabrication businesses can leverage the strengths of vertical band sawing machines to meet varied production requirements. Whether used for structural components, maintenance work, or custom assemblies, these machines offer a practical combination of precision and versatility that supports high-quality results across diverse applications.
In the metal fabrication and manufacturing sectors, cutting accuracy and operational flexibility are paramount. The vertical metal band sawing machine has steadily gained recognition as an indispensable tool for precision metal cutting. Its unique design and operational advantages make it a choice for many workshops and production lines focused on high-quality results and efficient material processing. Understanding the Vertical Metal Band Sawing MachineA vertical metal band sawing machine differs from its horizontal counterpart primarily in the orientation of its blade. The blade is positioned vertically, moving downwards through the workpiece which is clamped in place. This vertical motion offers certain ergonomic and functional advantages, especially when working with irregular or bulky metal pieces. The machine typically consists of a sturdy frame, a continuous loop blade made of high-speed steel or bi-metal, adjustable guides, and a powerful motor. Its design allows for both straight and angled cuts, with variable speed settings to accommodate different types of metals and thicknesses. Key Features and BenefitsSeveral features make the vertical metal band sawing machine particularly valuable across various metalworking applications: Space Efficiency: The vertical configuration often requires less floor space than horizontal machines, making it ideal for smaller workshops or crowded factory floors. Versatile Cutting Angles: The ability to tilt the blade or workpiece enables angled or miter cuts, expanding the range of possible cutting operations. Ease of Material Handling: Vertical band saws allow gravity-assisted feeding, simplifying the clamping and handling of large or heavy metal sections. Precision and Clean Cuts: The downward cutting action combined with steady clamping blade deflection, resulting in precise and smooth cuts with burrs. Adjustable Speeds: Variable speed controls accommodate a variety of metals, from soft aluminum to hardened steel, optimizing cut quality and blade life. Industry ApplicationsVertical metal band sawing machines find use across a diverse array of industries: Custom Metal Fabrication: Ideal for producing specialized parts with complex angles or shapes, often required in prototype development or small-batch production. Tool and Die Shops: Precision cuts are critical in making dies and molds; vertical band saws provide the accuracy needed. Automotive and Aerospace: Used for cutting metal sections where precise angles and finishes are necessary, particularly in assembling frames and components. Construction and Structural Fabrication: Cutting rebar, steel plates, and pipes at precise angles for fitting and welding. Maintenance and Repair Operations (MRO): The versatility and space-saving design make vertical band saws common in maintenance workshops for on-the-spot metal cutting needs. Maintenance: Ensuring PerformanceRegular maintenance is essential to sustain the performance and extend the service life of vertical metal band sawing machines. Key maintenance steps include: Blade Inspection and Replacement: Frequent examination of the blade for dullness, cracks, or missing teeth prevents poor cuts and potential machine damage. Replace or sharpen blades promptly. Proper Blade Tensioning: Ensuring the blade tension matches manufacturer recommendations avoids blade slippage and improves cut consistency. Guide and Bearing Checks: Inspect and lubricate guide rollers and bearings to maintain smooth blade tracking and reduce wear. Coolant System Upkeep: Keep coolant levels adequate and ensure the coolant delivery system is clean to prevent overheating and maintain blade sharpness. Cleaning: Remove metal chips and debris regularly to prevent buildup that can impair machine function or safety. Safety Feature Testing: Test emergency stops, guards, and switches regularly to ensure operator protection. Technological Innovations Enhancing Vertical Band SawsAs manufacturing technologies advance, vertical metal band sawing machines have incorporated several innovations: CNC Controls: Computerized control systems enable automation of cutting angles, feed rates, and blade speeds, enhancing repeatability and reducing operator error. Smart Sensors: Sensors monitor blade tension, motor load, and vibration, providing real-time data to anticipate maintenance needs and avoid unexpected breakdowns. Improved Blade Materials: Use of carbide-tipped or coated blades increases durability and cutting speed. Enhanced Ergonomics: Adjustable work tables, better control interfaces, and safety interlocks improve operator comfort and safety.
In the metal fabrication and manufacturing sectors, cutting accuracy and operational flexibility are paramount. The vertical metal band sawing machine has steadily gained recognition as an indispensable tool for precision metal cutting. Its unique design and operational advantages make it a choice for many workshops and production lines focused on high-quality results and efficient material processing. Understanding the Vertical Metal Band Sawing MachineA vertical metal band sawing machine differs from its horizontal counterpart primarily in the orientation of its blade. The blade is positioned vertically, moving downwards through the workpiece which is clamped in place. This vertical motion offers certain ergonomic and functional advantages, especially when working with irregular or bulky metal pieces. The machine typically consists of a sturdy frame, a continuous loop blade made of high-speed steel or bi-metal, adjustable guides, and a powerful motor. Its design allows for both straight and angled cuts, with variable speed settings to accommodate different types of metals and thicknesses. Key Features and BenefitsSeveral features make the vertical metal band sawing machine particularly valuable across various metalworking applications: Space Efficiency: The vertical configuration often requires less floor space than horizontal machines, making it ideal for smaller workshops or crowded factory floors. Versatile Cutting Angles: The ability to tilt the blade or workpiece enables angled or miter cuts, expanding the range of possible cutting operations. Ease of Material Handling: Vertical band saws allow gravity-assisted feeding, simplifying the clamping and handling of large or heavy metal sections. Precision and Clean Cuts: The downward cutting action combined with steady clamping blade deflection, resulting in precise and smooth cuts with burrs. Adjustable Speeds: Variable speed controls accommodate a variety of metals, from soft aluminum to hardened steel, optimizing cut quality and blade life. Industry ApplicationsVertical metal band sawing machines find use across a diverse array of industries: Custom Metal Fabrication: Ideal for producing specialized parts with complex angles or shapes, often required in prototype development or small-batch production. Tool and Die Shops: Precision cuts are critical in making dies and molds; vertical band saws provide the accuracy needed. Automotive and Aerospace: Used for cutting metal sections where precise angles and finishes are necessary, particularly in assembling frames and components. Construction and Structural Fabrication: Cutting rebar, steel plates, and pipes at precise angles for fitting and welding. Maintenance and Repair Operations (MRO): The versatility and space-saving design make vertical band saws common in maintenance workshops for on-the-spot metal cutting needs. Maintenance: Ensuring PerformanceRegular maintenance is essential to sustain the performance and extend the service life of vertical metal band sawing machines. Key maintenance steps include: Blade Inspection and Replacement: Frequent examination of the blade for dullness, cracks, or missing teeth prevents poor cuts and potential machine damage. Replace or sharpen blades promptly. Proper Blade Tensioning: Ensuring the blade tension matches manufacturer recommendations avoids blade slippage and improves cut consistency. Guide and Bearing Checks: Inspect and lubricate guide rollers and bearings to maintain smooth blade tracking and reduce wear. Coolant System Upkeep: Keep coolant levels adequate and ensure the coolant delivery system is clean to prevent overheating and maintain blade sharpness. Cleaning: Remove metal chips and debris regularly to prevent buildup that can impair machine function or safety. Safety Feature Testing: Test emergency stops, guards, and switches regularly to ensure operator protection. Technological Innovations Enhancing Vertical Band SawsAs manufacturing technologies advance, vertical metal band sawing machines have incorporated several innovations: CNC Controls: Computerized control systems enable automation of cutting angles, feed rates, and blade speeds, enhancing repeatability and reducing operator error. Smart Sensors: Sensors monitor blade tension, motor load, and vibration, providing real-time data to anticipate maintenance needs and avoid unexpected breakdowns. Improved Blade Materials: Use of carbide-tipped or coated blades increases durability and cutting speed. Enhanced Ergonomics: Adjustable work tables, better control interfaces, and safety interlocks improve operator comfort and safety.
In today’s fast-paced manufacturing landscape, precision, speed, and efficiency are paramount. The horizontal metal cutting band sawing machine has emerged as a vital solution for industries demanding accurate, reliable cuts of metal materials. From automotive to construction, aerospace to heavy machinery, this specialized equipment offers distinct advantages that are transforming metal fabrication workflows worldwide. This article explores the features, applications, maintenance essentials, and technological innovations driving the growing adoption of horizontal metal cutting band sawing machines. What Is a Horizontal Metal Cutting Band Sawing Machine?A horizontal metal cutting band sawing machine is designed with the saw blade positioned horizontally, enabling the cutting of metal stock in a straight, controlled manner. Unlike vertical saws, horizontal band saws clamp the material securely and bring the blade across the workpiece in a linear path. This configuration offers stability, precision, and the ability to handle larger and heavier metal pieces with ease. Typically, the blade consists of a continuous loop of high-speed steel or bi-metal that rotates around two wheels. The saw’s horizontal movement, combined with a powerful motor and adjustable feed rates, allows for clean, efficient cuts across various metal shapes and sizes. Key Features and BenefitsThe horizontal metal cutting band sawing machine is favored in industry for several reasons: High Cutting Accuracy: The horizontal design facilitates firm clamping of workpieces, vibrations and blade deflection. This ensures smooth, straight cuts with tight tolerances — essential in critical manufacturing processes. Versatility in Material Handling: These machines can cut through a wide range of metals, including stainless steel, aluminum, copper, and hardened alloys. Whether it’s round bars, square tubes, or irregular profiles, horizontal band saws offer adaptable cutting capabilities. Efficient Throughput: Automated feed systems allow continuous cutting without the need for manual repositioning, boosting productivity and reducing labor costs. Long Blade Life: The horizontal setup often incorporates advanced coolant delivery systems that reduce blade heat, extending blade life and improving cutting quality. Safety Features: Modern machines are equipped with blade guards, emergency stops, and automated shut-off systems to protect operators from injury. Industry ApplicationsHorizontal metal cutting band sawing machines serve multiple industries: Automotive Production: Used extensively for cutting raw metal stock into engine parts, chassis components, and exhaust systems with consistent precision. Construction and Structural Fabrication: Ideal for preparing steel beams, pipes, and reinforcing bars used in buildings, bridges, and infrastructure projects. Aerospace Manufacturing: Cutting aerospace-grade alloys and titanium with high accuracy is made easier with horizontal band saws, meeting stringent quality standards. Metal Fabrication Shops: Custom metal parts production benefits from the versatility and efficiency offered by horizontal band saws. Heavy Equipment Manufacturing: From agricultural machinery to mining equipment, large metal parts require the reliable cutting power of horizontal band saws. Maintenance Practices for Longevity and PerformanceTo maximize the value of a horizontal metal cutting band sawing machine, regular maintenance is crucial: Blade Inspection and Replacement: Daily checks for blade wear, cracks, and dullness help avoid poor cuts and machine damage. Replace or sharpen blades as necessary. Proper Blade Tensioning: Maintaining correct blade tension prevents slippage and uneven cutting. Coolant Management: Regularly refill and monitor coolant levels. Periodic flushing of the coolant system prevents clogging and contamination. Lubrication of Moving Parts: Greasing guide bearings, rollers, and drive components reduces wear and ensures smooth operation. Alignment Checks: Ensure blade wheels and guides remain properly aligned to prevent blade drift and improve cutting accuracy. Safety System Testing: Frequently test emergency stops, guards, and sensor systems to ensure operator protection. Technological Advancements Driving Industry AdoptionThe horizontal metal cutting band sawing machine industry is evolving with technological progress: CNC Integration: Computer numerical control allows precise automation of cutting lengths, angles, and feed rates, reducing human error and increasing repeatability. Smart Diagnostics: Embedded sensors monitor blade condition, motor load, and machine vibrations, enabling predictive maintenance and downtime. Energy-Efficient Motors: Modern machines feature energy-saving motors that lower operational costs and environmental impact.
In today’s fast-paced manufacturing landscape, precision, speed, and efficiency are paramount. The horizontal metal cutting band sawing machine has emerged as a vital solution for industries demanding accurate, reliable cuts of metal materials. From automotive to construction, aerospace to heavy machinery, this specialized equipment offers distinct advantages that are transforming metal fabrication workflows worldwide. This article explores the features, applications, maintenance essentials, and technological innovations driving the growing adoption of horizontal metal cutting band sawing machines. What Is a Horizontal Metal Cutting Band Sawing Machine?A horizontal metal cutting band sawing machine is designed with the saw blade positioned horizontally, enabling the cutting of metal stock in a straight, controlled manner. Unlike vertical saws, horizontal band saws clamp the material securely and bring the blade across the workpiece in a linear path. This configuration offers stability, precision, and the ability to handle larger and heavier metal pieces with ease. Typically, the blade consists of a continuous loop of high-speed steel or bi-metal that rotates around two wheels. The saw’s horizontal movement, combined with a powerful motor and adjustable feed rates, allows for clean, efficient cuts across various metal shapes and sizes. Key Features and BenefitsThe horizontal metal cutting band sawing machine is favored in industry for several reasons: High Cutting Accuracy: The horizontal design facilitates firm clamping of workpieces, vibrations and blade deflection. This ensures smooth, straight cuts with tight tolerances — essential in critical manufacturing processes. Versatility in Material Handling: These machines can cut through a wide range of metals, including stainless steel, aluminum, copper, and hardened alloys. Whether it’s round bars, square tubes, or irregular profiles, horizontal band saws offer adaptable cutting capabilities. Efficient Throughput: Automated feed systems allow continuous cutting without the need for manual repositioning, boosting productivity and reducing labor costs. Long Blade Life: The horizontal setup often incorporates advanced coolant delivery systems that reduce blade heat, extending blade life and improving cutting quality. Safety Features: Modern machines are equipped with blade guards, emergency stops, and automated shut-off systems to protect operators from injury. Industry ApplicationsHorizontal metal cutting band sawing machines serve multiple industries: Automotive Production: Used extensively for cutting raw metal stock into engine parts, chassis components, and exhaust systems with consistent precision. Construction and Structural Fabrication: Ideal for preparing steel beams, pipes, and reinforcing bars used in buildings, bridges, and infrastructure projects. Aerospace Manufacturing: Cutting aerospace-grade alloys and titanium with high accuracy is made easier with horizontal band saws, meeting stringent quality standards. Metal Fabrication Shops: Custom metal parts production benefits from the versatility and efficiency offered by horizontal band saws. Heavy Equipment Manufacturing: From agricultural machinery to mining equipment, large metal parts require the reliable cutting power of horizontal band saws. Maintenance Practices for Longevity and PerformanceTo maximize the value of a horizontal metal cutting band sawing machine, regular maintenance is crucial: Blade Inspection and Replacement: Daily checks for blade wear, cracks, and dullness help avoid poor cuts and machine damage. Replace or sharpen blades as necessary. Proper Blade Tensioning: Maintaining correct blade tension prevents slippage and uneven cutting. Coolant Management: Regularly refill and monitor coolant levels. Periodic flushing of the coolant system prevents clogging and contamination. Lubrication of Moving Parts: Greasing guide bearings, rollers, and drive components reduces wear and ensures smooth operation. Alignment Checks: Ensure blade wheels and guides remain properly aligned to prevent blade drift and improve cutting accuracy. Safety System Testing: Frequently test emergency stops, guards, and sensor systems to ensure operator protection. Technological Advancements Driving Industry AdoptionThe horizontal metal cutting band sawing machine industry is evolving with technological progress: CNC Integration: Computer numerical control allows precise automation of cutting lengths, angles, and feed rates, reducing human error and increasing repeatability. Smart Diagnostics: Embedded sensors monitor blade condition, motor load, and machine vibrations, enabling predictive maintenance and downtime. Energy-Efficient Motors: Modern machines feature energy-saving motors that lower operational costs and environmental impact.
In the manufacturing and metalworking industries, the metal cutting band sawing machine has established itself as an essential tool for efficient and precise cutting operations. Renowned for its versatility, durability, and ability to handle a wide range of metal types and sizes, this specialized machine plays a pivotal role in fabricating components, shaping raw materials, and streamlining production workflows. As demand grows for higher-quality metal products and faster turnaround times, understanding the features, applications, and maintenance of metal cutting band sawing machines is critical for industry players aiming to stay competitive. What is a Metal Cutting Band Sawing Machine?A metal cutting band sawing machine is designed specifically to cut metals of various hardness and thicknesses using a continuous loop blade. Unlike traditional saws, the band saw utilizes a thin, flexible blade made of high-speed steel or bi-metal that moves continuously around two wheels, providing smooth and uniform cuts. Its capability to cut irregular shapes, straight lines, and even curved sections with material wastage makes it highly valuable in metal fabrication shops, automotive parts manufacturing, aerospace, and heavy machinery industries. Key Features Driving Industry DemandSeveral features distinguish metal cutting band sawing machines and contribute to their widespread adoption: Blade Versatility: Metal band saw blades come in different tooth configurations and materials tailored to specific metal types such as stainless steel, aluminum, copper, or hardened steel. This allows operators to select the blade for the job, balancing cutting speed and finish quality. Automatic Feeding and Cutting: Modern metal cutting band sawing machines often feature programmable controls for automatic material feeding, cutting length adjustment, and blade speed regulation. This automation reduces operator fatigue, enhances precision, and increases throughput. Coolant Systems: Integrated coolant delivery systems are critical in metal cutting applications to reduce blade heat buildup, prevent metal warping, and prolong blade life. These systems typically spray coolant directly onto the cutting zone during operation. Robust Frame and Drive System: To handle the stresses of metal cutting, these machines are constructed with heavy-duty steel frames and powerful motors, ensuring stability and consistent cutting performance even under demanding workloads. Applications Across IndustriesMetal cutting band sawing machines are versatile tools that serve a broad spectrum of industries: Automotive Manufacturing: From cutting engine components to exhaust systems, band saws help produce precise metal parts needed for vehicle assembly. Construction and Infrastructure: Fabricating structural steel beams, pipes, and reinforcement bars often involves band sawing to ensure clean, accurate cuts. Aerospace: High-precision metal cutting band saws are used to cut exotic alloys and titanium, critical in aerospace components. Metal Fabrication Shops: Custom metal parts production benefits greatly from the flexibility and efficiency of band sawing technology. Practices for Machine PerformanceTo keep metal cutting band sawing machines operating at peak efficiency, several practices have emerged: Proper Blade Selection and Maintenance: Using the correct blade type and maintaining sharpness through timely replacement or resharpening is crucial to prevent overheating and maintain cut quality. Routine Cleaning and Lubrication: Regularly cleaning metal chips and debris from the blade and machine components helps avoid mechanical issues and corrosion. Lubricating moving parts reduces friction and wear. Monitoring Blade Tension and Alignment: Ensuring that the blade tension is and that blade wheels are aligned prevents blade drift and breakage. Using Coolants Efficiently: Maintaining coolant levels and ensuring proper flow can dramatically extend blade life and improve cutting precision. Challenges and Technological InnovationsDespite their advantages, metal cutting band sawing machines face challenges such as blade wear, heat generation, and material waste. To address these, manufacturers are investing in technological innovations including: Advanced Blade Materials: Development of carbide-tipped and coated blades enhance durability and cutting speed. CNC Integration: Computer numerical control (CNC) systems enable precise control over cutting parameters, allowing complex cuts with human intervention. Smart Monitoring Systems: Sensors embedded in machines can track blade condition, machine vibrations, and temperature to predict maintenance needs, reducing unplanned downtime.
In the manufacturing and metalworking industries, the metal cutting band sawing machine has established itself as an essential tool for efficient and precise cutting operations. Renowned for its versatility, durability, and ability to handle a wide range of metal types and sizes, this specialized machine plays a pivotal role in fabricating components, shaping raw materials, and streamlining production workflows. As demand grows for higher-quality metal products and faster turnaround times, understanding the features, applications, and maintenance of metal cutting band sawing machines is critical for industry players aiming to stay competitive. What is a Metal Cutting Band Sawing Machine?A metal cutting band sawing machine is designed specifically to cut metals of various hardness and thicknesses using a continuous loop blade. Unlike traditional saws, the band saw utilizes a thin, flexible blade made of high-speed steel or bi-metal that moves continuously around two wheels, providing smooth and uniform cuts. Its capability to cut irregular shapes, straight lines, and even curved sections with material wastage makes it highly valuable in metal fabrication shops, automotive parts manufacturing, aerospace, and heavy machinery industries. Key Features Driving Industry DemandSeveral features distinguish metal cutting band sawing machines and contribute to their widespread adoption: Blade Versatility: Metal band saw blades come in different tooth configurations and materials tailored to specific metal types such as stainless steel, aluminum, copper, or hardened steel. This allows operators to select the blade for the job, balancing cutting speed and finish quality. Automatic Feeding and Cutting: Modern metal cutting band sawing machines often feature programmable controls for automatic material feeding, cutting length adjustment, and blade speed regulation. This automation reduces operator fatigue, enhances precision, and increases throughput. Coolant Systems: Integrated coolant delivery systems are critical in metal cutting applications to reduce blade heat buildup, prevent metal warping, and prolong blade life. These systems typically spray coolant directly onto the cutting zone during operation. Robust Frame and Drive System: To handle the stresses of metal cutting, these machines are constructed with heavy-duty steel frames and powerful motors, ensuring stability and consistent cutting performance even under demanding workloads. Applications Across IndustriesMetal cutting band sawing machines are versatile tools that serve a broad spectrum of industries: Automotive Manufacturing: From cutting engine components to exhaust systems, band saws help produce precise metal parts needed for vehicle assembly. Construction and Infrastructure: Fabricating structural steel beams, pipes, and reinforcement bars often involves band sawing to ensure clean, accurate cuts. Aerospace: High-precision metal cutting band saws are used to cut exotic alloys and titanium, critical in aerospace components. Metal Fabrication Shops: Custom metal parts production benefits greatly from the flexibility and efficiency of band sawing technology. Practices for Machine PerformanceTo keep metal cutting band sawing machines operating at peak efficiency, several practices have emerged: Proper Blade Selection and Maintenance: Using the correct blade type and maintaining sharpness through timely replacement or resharpening is crucial to prevent overheating and maintain cut quality. Routine Cleaning and Lubrication: Regularly cleaning metal chips and debris from the blade and machine components helps avoid mechanical issues and corrosion. Lubricating moving parts reduces friction and wear. Monitoring Blade Tension and Alignment: Ensuring that the blade tension is and that blade wheels are aligned prevents blade drift and breakage. Using Coolants Efficiently: Maintaining coolant levels and ensuring proper flow can dramatically extend blade life and improve cutting precision. Challenges and Technological InnovationsDespite their advantages, metal cutting band sawing machines face challenges such as blade wear, heat generation, and material waste. To address these, manufacturers are investing in technological innovations including: Advanced Blade Materials: Development of carbide-tipped and coated blades enhance durability and cutting speed. CNC Integration: Computer numerical control (CNC) systems enable precise control over cutting parameters, allowing complex cuts with human intervention. Smart Monitoring Systems: Sensors embedded in machines can track blade condition, machine vibrations, and temperature to predict maintenance needs, reducing unplanned downtime.
In the metalworking and woodworking industries, the band sawing machine is a cornerstone of precise and efficient cutting. Known for its versatility, high performance, and ability to produce consistent results across a wide range of materials, the band sawing machine is heavily relied upon in factories, workshops, and production lines. However, like any industrial-grade equipment, its productivity and longevity are directly tied to proper maintenance. This article explores industry practices, preventive measures, and the technological solutions for maintaining a band sawing machine to ensure performance and downtime. Why Maintenance Matters for Band Sawing MachinesA band sawing machine, whether used in cutting metal, wood, or plastic, operates under demanding conditions. Blades rotate at high speeds and endure significant stress, which can cause wear and tear if not properly maintained. Poor maintenance leads to imprecise cuts, blade breakage, overheating, and ultimately expensive downtime. Regular and thorough maintenance not only prolongs the machine’s life but also improves safety, accuracy, and overall operational efficiency. Daily Maintenance ChecklistRoutine daily checks are the line of defense in maintaining a band sawing machine. Operators should start each shift with a basic inspection to ensure that key components are in good working condition: Blade Condition: Inspect the blade for cracks, dull edges, or uneven wear. Replace or sharpen the blade as needed to avoid poor cutting performance and machine strain. Blade Tension: Verify that the blade tension is set to the manufacturer's recommended levels. Improper tension can to blade slippage or breakage. Coolant Levels: Ensure coolant reservoirs are filled and that the coolant flow is consistent. Adequate cooling is essential for blade longevity and heat control during cutting. Guide Bearings and Rollers: Check the guide bearings for smooth rotation and proper alignment. Worn or misaligned guides can cause the blade to drift, to inaccurate cuts. Cleanliness: Remove chips, dust, and debris from the machine surface, especially around the blade and guide areas. Cleanliness prevents buildup that can interfere with performance. Weekly and Monthly MaintenanceWhile daily maintenance focuses on immediate operational readiness, weekly and monthly checks address long-term wear and mechanical integrity: Lubrication: Grease all moving parts, including the blade guides, bearings, and pivot points. Consistent lubrication reduces friction and wear. Hydraulic System: For hydraulic band sawing machines, inspect hoses and fittings for leaks. Check fluid levels and replace filters periodically to maintain smooth operation. Drive Belt and Pulley Inspection: Examine belts for signs of wear, cracks, or slackness. Proper belt tension ensures efficient power transmission from the motor to the blade wheels. Blade Wheel Alignment: Verify that the upper and lower blade wheels are correctly aligned. Misalignment can cause premature blade wear and erratic cutting. Coolant System Flush: Flush and clean the coolant system at least once a month to prevent contamination and bacteria buildup, which can compromise cooling efficiency. Safety Mechanisms and Electrical SystemsBand sawing machines come equipped with safety features such as emergency stop buttons, blade guards, and automatic shut-off sensors. Regular testing of these features is crucial for workplace safety: Test Emergency Stops: Ensure that emergency stop buttons are functioning and accessible. Non-functional safety controls pose serious hazards. Check Wiring and Switches: Inspect all electrical connections, switches, and control panels for signs of damage or loose connections. Damaged wiring should be repaired by qualified personnel immediately. Blade Guard Adjustments: Make sure blade guards are secure and positioned properly to minimize operator exposure to moving parts. Record-Keeping and Predictive MaintenanceModern band sawing machines are often equipped with digital displays and diagnostic systems that log operating data. Maintaining a detailed maintenance log helps track wear patterns, identify recurring issues, and plan predictive maintenance activities. Predictive maintenance, supported by sensors and software, allows operators to monitor vibration, temperature, and blade usage in real-time. These data points can trigger alerts when components show signs of imminent failure, helping to prevent unplanned downtime.
In the metalworking and woodworking industries, the band sawing machine is a cornerstone of precise and efficient cutting. Known for its versatility, high performance, and ability to produce consistent results across a wide range of materials, the band sawing machine is heavily relied upon in factories, workshops, and production lines. However, like any industrial-grade equipment, its productivity and longevity are directly tied to proper maintenance. This article explores industry practices, preventive measures, and the technological solutions for maintaining a band sawing machine to ensure performance and downtime. Why Maintenance Matters for Band Sawing MachinesA band sawing machine, whether used in cutting metal, wood, or plastic, operates under demanding conditions. Blades rotate at high speeds and endure significant stress, which can cause wear and tear if not properly maintained. Poor maintenance leads to imprecise cuts, blade breakage, overheating, and ultimately expensive downtime. Regular and thorough maintenance not only prolongs the machine’s life but also improves safety, accuracy, and overall operational efficiency. Daily Maintenance ChecklistRoutine daily checks are the line of defense in maintaining a band sawing machine. Operators should start each shift with a basic inspection to ensure that key components are in good working condition: Blade Condition: Inspect the blade for cracks, dull edges, or uneven wear. Replace or sharpen the blade as needed to avoid poor cutting performance and machine strain. Blade Tension: Verify that the blade tension is set to the manufacturer's recommended levels. Improper tension can to blade slippage or breakage. Coolant Levels: Ensure coolant reservoirs are filled and that the coolant flow is consistent. Adequate cooling is essential for blade longevity and heat control during cutting. Guide Bearings and Rollers: Check the guide bearings for smooth rotation and proper alignment. Worn or misaligned guides can cause the blade to drift, to inaccurate cuts. Cleanliness: Remove chips, dust, and debris from the machine surface, especially around the blade and guide areas. Cleanliness prevents buildup that can interfere with performance. Weekly and Monthly MaintenanceWhile daily maintenance focuses on immediate operational readiness, weekly and monthly checks address long-term wear and mechanical integrity: Lubrication: Grease all moving parts, including the blade guides, bearings, and pivot points. Consistent lubrication reduces friction and wear. Hydraulic System: For hydraulic band sawing machines, inspect hoses and fittings for leaks. Check fluid levels and replace filters periodically to maintain smooth operation. Drive Belt and Pulley Inspection: Examine belts for signs of wear, cracks, or slackness. Proper belt tension ensures efficient power transmission from the motor to the blade wheels. Blade Wheel Alignment: Verify that the upper and lower blade wheels are correctly aligned. Misalignment can cause premature blade wear and erratic cutting. Coolant System Flush: Flush and clean the coolant system at least once a month to prevent contamination and bacteria buildup, which can compromise cooling efficiency. Safety Mechanisms and Electrical SystemsBand sawing machines come equipped with safety features such as emergency stop buttons, blade guards, and automatic shut-off sensors. Regular testing of these features is crucial for workplace safety: Test Emergency Stops: Ensure that emergency stop buttons are functioning and accessible. Non-functional safety controls pose serious hazards. Check Wiring and Switches: Inspect all electrical connections, switches, and control panels for signs of damage or loose connections. Damaged wiring should be repaired by qualified personnel immediately. Blade Guard Adjustments: Make sure blade guards are secure and positioned properly to minimize operator exposure to moving parts. Record-Keeping and Predictive MaintenanceModern band sawing machines are often equipped with digital displays and diagnostic systems that log operating data. Maintaining a detailed maintenance log helps track wear patterns, identify recurring issues, and plan predictive maintenance activities. Predictive maintenance, supported by sensors and software, allows operators to monitor vibration, temperature, and blade usage in real-time. These data points can trigger alerts when components show signs of imminent failure, helping to prevent unplanned downtime.
In the ever-evolving landscape of manufacturing, precision and efficiency are critical factors that determine the success of any business. One key component in achieving these goals, especially in cutting and shaping materials, is the band saw blade. As industries continue to demand faster, more accurate cutting methods, the band saw blade has become indispensable in a variety of sectors, ranging from metalworking to woodworking, plastics, and even food processing. What is a Band Saw Blade?A band saw blade is a long, continuous loop of toothed steel that is used to cut through materials with a band saw machine. It typically runs over two or more wheels, with one wheel being powered by a motor to drive the blade, while the other is used for tensioning. The band saw blade can vary in size, tooth type, and material, depending on the specific requirements of the cutting job. These blades can be designed for cutting wood, metal, plastic, or even delicate materials like food and textiles, making them one of the versatile cutting tools available in industrial settings. The versatility and precision of the band saw blade have made it a popular choice across various industries, from automotive manufacturing to construction, and even in the production of consumer goods. Why Band Saw Blades Are Crucial in Manufacturing1. Precision CuttingThe ability to make precise, smooth cuts is one of the primary reasons the band saw blade is so widely used in manufacturing. Unlike traditional cutting methods, such as hacksaws or circular saws, which often leave rough edges or require additional finishing, the band saw blade delivers clean and accurate cuts. This feature is essential in industries that require high precision, such as aerospace, automotive, and electronics manufacturing. Furthermore, the band saw blade offers the ability to make intricate cuts, such as curved or irregular shapes, with minimal effort. This flexibility is a significant advantage in industries like custom fabrication, furniture making, and even sculpting. 2. Versatility Across MaterialsThe band saw blade is incredibly versatile when it comes to the materials it can cut. Different types of blades are designed for cutting specific materials, such as steel, aluminum, wood, plastics, and even food items. By choosing the correct blade for the material being cut, manufacturers can optimize the cutting process, ensuring that each job is completed efficiently and accurately. For example, blades with high tooth density and bi-metallic construction are often used for cutting hard metals, while blades with wider teeth are used for softer materials like wood. This versatility means that industries of all kinds can benefit from using a band saw blade, as it can adapt to various cutting needs. 3. Increased Efficiency and SpeedManufacturers today are always looking for ways to reduce production time and increase efficiency. The band saw blade plays a critical role in achieving these goals. With its ability to cut through materials quickly and accurately, the band saw blade minimizes the need for rework or secondary operations. This is especially valuable in high-volume production settings where time is of the essence. Additionally, modern band saw machines are equipped with features that increase cutting speed, such as automatic feed mechanisms, variable speed controls, and advanced tensioning systems. This allows operators to complete cuts faster and with greater consistency, which improves overall productivity and reduces downtime. 4. Minimal Material WasteAnother significant advantage of using a band saw blade is its ability to reduce material waste. The thin, continuous cutting edge of the blade creates minimal kerf (the amount of material removed during the cut), meaning that more of the material remains intact and can be used for other purposes. In industries where material costs are high, such as metalworking and plastics fabrication, this reduction in waste can translate into significant cost savings. Moreover, the clean cuts made by the band saw blade eliminate the need for additional finishing steps, further minimizing waste and improving the overall efficiency of the manufacturing process.
In the ever-evolving landscape of manufacturing, precision and efficiency are critical factors that determine the success of any business. One key component in achieving these goals, especially in cutting and shaping materials, is the band saw blade. As industries continue to demand faster, more accurate cutting methods, the band saw blade has become indispensable in a variety of sectors, ranging from metalworking to woodworking, plastics, and even food processing. What is a Band Saw Blade?A band saw blade is a long, continuous loop of toothed steel that is used to cut through materials with a band saw machine. It typically runs over two or more wheels, with one wheel being powered by a motor to drive the blade, while the other is used for tensioning. The band saw blade can vary in size, tooth type, and material, depending on the specific requirements of the cutting job. These blades can be designed for cutting wood, metal, plastic, or even delicate materials like food and textiles, making them one of the versatile cutting tools available in industrial settings. The versatility and precision of the band saw blade have made it a popular choice across various industries, from automotive manufacturing to construction, and even in the production of consumer goods. Why Band Saw Blades Are Crucial in Manufacturing1. Precision CuttingThe ability to make precise, smooth cuts is one of the primary reasons the band saw blade is so widely used in manufacturing. Unlike traditional cutting methods, such as hacksaws or circular saws, which often leave rough edges or require additional finishing, the band saw blade delivers clean and accurate cuts. This feature is essential in industries that require high precision, such as aerospace, automotive, and electronics manufacturing. Furthermore, the band saw blade offers the ability to make intricate cuts, such as curved or irregular shapes, with minimal effort. This flexibility is a significant advantage in industries like custom fabrication, furniture making, and even sculpting. 2. Versatility Across MaterialsThe band saw blade is incredibly versatile when it comes to the materials it can cut. Different types of blades are designed for cutting specific materials, such as steel, aluminum, wood, plastics, and even food items. By choosing the correct blade for the material being cut, manufacturers can optimize the cutting process, ensuring that each job is completed efficiently and accurately. For example, blades with high tooth density and bi-metallic construction are often used for cutting hard metals, while blades with wider teeth are used for softer materials like wood. This versatility means that industries of all kinds can benefit from using a band saw blade, as it can adapt to various cutting needs. 3. Increased Efficiency and SpeedManufacturers today are always looking for ways to reduce production time and increase efficiency. The band saw blade plays a critical role in achieving these goals. With its ability to cut through materials quickly and accurately, the band saw blade minimizes the need for rework or secondary operations. This is especially valuable in high-volume production settings where time is of the essence. Additionally, modern band saw machines are equipped with features that increase cutting speed, such as automatic feed mechanisms, variable speed controls, and advanced tensioning systems. This allows operators to complete cuts faster and with greater consistency, which improves overall productivity and reduces downtime. 4. Minimal Material WasteAnother significant advantage of using a band saw blade is its ability to reduce material waste. The thin, continuous cutting edge of the blade creates minimal kerf (the amount of material removed during the cut), meaning that more of the material remains intact and can be used for other purposes. In industries where material costs are high, such as metalworking and plastics fabrication, this reduction in waste can translate into significant cost savings. Moreover, the clean cuts made by the band saw blade eliminate the need for additional finishing steps, further minimizing waste and improving the overall efficiency of the manufacturing process.
In the world of metalworking, wood processing, and even in the production of complex plastic components, the angle band saw machine has become an indispensable tool for achieving high precision and efficiency. As industries demand greater accuracy and faster production times, the angle band saw machine has stepped in to meet these needs, offering cutting performance and versatility across various applications. With technological advancements pushing the boundaries of what's possible, this machinery has evolved into a cutting-edge solution for modern manufacturing. What is an Angle Band Saw Machine?The angle band saw machine is a specialized cutting tool designed to make accurate cuts in materials such as metal, wood, and plastic. The key feature that distinguishes an angle band saw from a traditional band saw is its ability to cut at different angles, making it highly adaptable for a wide range of tasks. The machine consists of a continuous loop of toothed steel band that moves over two wheels and is powered by a motor. The saw blade is adjustable to different angles, allowing for precise crosscuts, miter cuts, and compound cuts at various angles. By using this saw, operators can easily cut through materials in ways that would be impossible with standard cutting machines. For industries requiring highly precise cuts or those working with materials of varying thicknesses, the angle band saw machine is a game-changer. Why Are Angle Band Saw Machines So Popular?1. Precision and AccuracyOne of the biggest advantages of using an angle band saw machine is the high level of precision it provides. Unlike traditional cutting methods that may leave rough edges or require additional finishing steps, the angle band saw machine ensures that each cut is smooth and accurate. This is especially important in industries like aerospace, automotive manufacturing, and construction, where even the smallest imperfections can affect the integrity of the final product. The ability to adjust the cutting angle allows operators to make intricate cuts at precise angles without the need for multiple setups or complex machinery. This not only saves time but also reduces the potential for errors, to higher-quality outputs. 2. Versatility Across MaterialsThe angle band saw machine is not limited to just one type of material. It is highly versatile and can be used to cut a wide variety of substances, from metals like steel, aluminum, and stainless steel, to softer materials like wood and plastics. This flexibility makes it an ideal solution for a diverse range of industries, from construction to furniture making, to custom metalworking shops. The machine's ability to handle different material types with ease and efficiency has made it the go-to choice for businesses that work with multiple materials on a daily basis. Whether it’s cutting thick metal pipes or intricate wooden components, the angle band saw machine can handle it all. 3. Increased Efficiency and ProductivitySpeed is crucial in the modern manufacturing landscape, and the angle band saw machine delivers impressive cutting speeds. Traditional cutting methods, such as manual saws or even older band saws, require significant downtime for setup and adjustments. However, with the angle band saw machine, operators can quickly adjust cutting angles and settings, reducing the amount of time spent on setup and allowing for faster production cycles. Additionally, the machine’s ability to make precise cuts consistently reduces the need for rework, further boosting productivity. In industries where high output is required, such as in automotive parts manufacturing or mass production of metal components, this efficiency is invaluable. 4. Reduced Material WasteWaste reduction is a major concern for manufacturers across all industries. In addition to increasing productivity, the angle band saw machine also contributes to minimizing material waste. Traditional cutting methods often result in irregular cuts that may require reprocessing or scrapping of materials. In contrast, the precision of the angle band saw machine allows for cleaner cuts, ensuring that as much of the material as possible is usable. This reduction in waste not only lowers material costs but also makes the process more environmentally friendly, aligning with the growing demand for sustainable manufacturing practices.
In the world of metalworking, wood processing, and even in the production of complex plastic components, the angle band saw machine has become an indispensable tool for achieving high precision and efficiency. As industries demand greater accuracy and faster production times, the angle band saw machine has stepped in to meet these needs, offering cutting performance and versatility across various applications. With technological advancements pushing the boundaries of what's possible, this machinery has evolved into a cutting-edge solution for modern manufacturing. What is an Angle Band Saw Machine?The angle band saw machine is a specialized cutting tool designed to make accurate cuts in materials such as metal, wood, and plastic. The key feature that distinguishes an angle band saw from a traditional band saw is its ability to cut at different angles, making it highly adaptable for a wide range of tasks. The machine consists of a continuous loop of toothed steel band that moves over two wheels and is powered by a motor. The saw blade is adjustable to different angles, allowing for precise crosscuts, miter cuts, and compound cuts at various angles. By using this saw, operators can easily cut through materials in ways that would be impossible with standard cutting machines. For industries requiring highly precise cuts or those working with materials of varying thicknesses, the angle band saw machine is a game-changer. Why Are Angle Band Saw Machines So Popular?1. Precision and AccuracyOne of the biggest advantages of using an angle band saw machine is the high level of precision it provides. Unlike traditional cutting methods that may leave rough edges or require additional finishing steps, the angle band saw machine ensures that each cut is smooth and accurate. This is especially important in industries like aerospace, automotive manufacturing, and construction, where even the smallest imperfections can affect the integrity of the final product. The ability to adjust the cutting angle allows operators to make intricate cuts at precise angles without the need for multiple setups or complex machinery. This not only saves time but also reduces the potential for errors, to higher-quality outputs. 2. Versatility Across MaterialsThe angle band saw machine is not limited to just one type of material. It is highly versatile and can be used to cut a wide variety of substances, from metals like steel, aluminum, and stainless steel, to softer materials like wood and plastics. This flexibility makes it an ideal solution for a diverse range of industries, from construction to furniture making, to custom metalworking shops. The machine's ability to handle different material types with ease and efficiency has made it the go-to choice for businesses that work with multiple materials on a daily basis. Whether it’s cutting thick metal pipes or intricate wooden components, the angle band saw machine can handle it all. 3. Increased Efficiency and ProductivitySpeed is crucial in the modern manufacturing landscape, and the angle band saw machine delivers impressive cutting speeds. Traditional cutting methods, such as manual saws or even older band saws, require significant downtime for setup and adjustments. However, with the angle band saw machine, operators can quickly adjust cutting angles and settings, reducing the amount of time spent on setup and allowing for faster production cycles. Additionally, the machine’s ability to make precise cuts consistently reduces the need for rework, further boosting productivity. In industries where high output is required, such as in automotive parts manufacturing or mass production of metal components, this efficiency is invaluable. 4. Reduced Material WasteWaste reduction is a major concern for manufacturers across all industries. In addition to increasing productivity, the angle band saw machine also contributes to minimizing material waste. Traditional cutting methods often result in irregular cuts that may require reprocessing or scrapping of materials. In contrast, the precision of the angle band saw machine allows for cleaner cuts, ensuring that as much of the material as possible is usable. This reduction in waste not only lowers material costs but also makes the process more environmentally friendly, aligning with the growing demand for sustainable manufacturing practices.
In the realm of industrial cutting tools, the horizontal die steel band saw machine has emerged as one of the powerful and efficient machines available for precision metal cutting. As industries become increasingly focused on automation and precision, the need for tools that can provide high-quality, reliable results has never been more critical. The horizontal die steel band saw machine has proven to be essential in meeting these demands across a variety of sectors, from automotive manufacturing to aerospace and steel fabrication. What is a Horizontal Die Steel Band Saw Machine?The horizontal die steel band saw machine is a type of band saw used primarily for cutting large metal workpieces, such as steel bars, billets, and other heavy-duty materials. It operates using a continuous loop of a toothed steel blade that moves across the material, powered by an electric motor. The horizontal design allows for greater stability and precision when cutting large pieces of metal. This configuration makes it ideal for applications that require cutting through thick or dense materials with accuracy and efficiency. The design of the horizontal die steel band saw machine is engineered to provide consistent cutting results, reducing material wastage and ensuring minimal downtime during operations. This combination of functionality and efficiency is what makes the machine an indispensable asset for metalworking industries. Key Features of the Horizontal Die Steel Band Saw Machine1. Precise Metal CuttingOne of the key advantages of using the horizontal die steel band saw machine is its ability to perform precise metal cutting. The machine’s ability to make accurate, straight cuts through hard materials like steel makes it ideal for industries that require a high level of precision, such as aerospace, automotive, and construction. Whether cutting metal bars, pipes, or other large components, the machine delivers clean, straight cuts with minimal effort. Furthermore, the continuous band blade of the machine allows it to cut through thicker materials than traditional cutting methods, enhancing its versatility. The precision achieved with a horizontal die steel band saw machine eliminates the need for additional processing or finishing, saving both time and money in production. 2. High EfficiencyEfficiency is paramount in manufacturing, and the horizontal die steel band saw machine is designed to increase throughput without compromising on quality. These machines are equipped with advanced features such as automatic feed mechanisms and variable cutting speeds, which allow operators to control the cutting process with great precision. The automatic functions of the horizontal die steel band saw machine enable it to cut large volumes of material with minimal manual intervention, reducing labor costs and increasing productivity. With faster cutting times and higher material throughput, manufacturers can achieve higher output levels, to increased profits and reduced production costs. The machine’s advanced design also reduces the amount of time spent on maintenance, as the band saw operates efficiently for longer periods, requiring less frequent downtime for repairs. 3. Durability and ReliabilityDurability is a crucial factor in any industrial machinery, and the horizontal die steel band saw machine excels in this regard. These machines are built to withstand the rigors of high-demand manufacturing environments, where heavy-duty materials and extended operational hours are the norm. The robust construction of the machine, combined with its high-performance components, ensures that it can operate continuously for long periods without significant wear and tear. Moreover, the horizontal die steel band saw machine is designed to require minimal maintenance, which helps reduce operating costs over time. With proper care, these machines can last for many years, offering manufacturers a long-term investment that provides return on investment. 4. Versatility in Material HandlingOne of the standout features of the horizontal die steel band saw machine is its versatility in handling a wide range of materials. While it is primarily used for cutting steel and other metals, it can also be adapted to cut softer materials like aluminum, brass, and copper. The machine is capable of cutting materials in various shapes and sizes, making it ideal for industries such as construction, mining, and automotive manufacturing, where different materials are used for different applications.
In the realm of industrial cutting tools, the horizontal die steel band saw machine has emerged as one of the powerful and efficient machines available for precision metal cutting. As industries become increasingly focused on automation and precision, the need for tools that can provide high-quality, reliable results has never been more critical. The horizontal die steel band saw machine has proven to be essential in meeting these demands across a variety of sectors, from automotive manufacturing to aerospace and steel fabrication. What is a Horizontal Die Steel Band Saw Machine?The horizontal die steel band saw machine is a type of band saw used primarily for cutting large metal workpieces, such as steel bars, billets, and other heavy-duty materials. It operates using a continuous loop of a toothed steel blade that moves across the material, powered by an electric motor. The horizontal design allows for greater stability and precision when cutting large pieces of metal. This configuration makes it ideal for applications that require cutting through thick or dense materials with accuracy and efficiency. The design of the horizontal die steel band saw machine is engineered to provide consistent cutting results, reducing material wastage and ensuring minimal downtime during operations. This combination of functionality and efficiency is what makes the machine an indispensable asset for metalworking industries. Key Features of the Horizontal Die Steel Band Saw Machine1. Precise Metal CuttingOne of the key advantages of using the horizontal die steel band saw machine is its ability to perform precise metal cutting. The machine’s ability to make accurate, straight cuts through hard materials like steel makes it ideal for industries that require a high level of precision, such as aerospace, automotive, and construction. Whether cutting metal bars, pipes, or other large components, the machine delivers clean, straight cuts with minimal effort. Furthermore, the continuous band blade of the machine allows it to cut through thicker materials than traditional cutting methods, enhancing its versatility. The precision achieved with a horizontal die steel band saw machine eliminates the need for additional processing or finishing, saving both time and money in production. 2. High EfficiencyEfficiency is paramount in manufacturing, and the horizontal die steel band saw machine is designed to increase throughput without compromising on quality. These machines are equipped with advanced features such as automatic feed mechanisms and variable cutting speeds, which allow operators to control the cutting process with great precision. The automatic functions of the horizontal die steel band saw machine enable it to cut large volumes of material with minimal manual intervention, reducing labor costs and increasing productivity. With faster cutting times and higher material throughput, manufacturers can achieve higher output levels, to increased profits and reduced production costs. The machine’s advanced design also reduces the amount of time spent on maintenance, as the band saw operates efficiently for longer periods, requiring less frequent downtime for repairs. 3. Durability and ReliabilityDurability is a crucial factor in any industrial machinery, and the horizontal die steel band saw machine excels in this regard. These machines are built to withstand the rigors of high-demand manufacturing environments, where heavy-duty materials and extended operational hours are the norm. The robust construction of the machine, combined with its high-performance components, ensures that it can operate continuously for long periods without significant wear and tear. Moreover, the horizontal die steel band saw machine is designed to require minimal maintenance, which helps reduce operating costs over time. With proper care, these machines can last for many years, offering manufacturers a long-term investment that provides return on investment. 4. Versatility in Material HandlingOne of the standout features of the horizontal die steel band saw machine is its versatility in handling a wide range of materials. While it is primarily used for cutting steel and other metals, it can also be adapted to cut softer materials like aluminum, brass, and copper. The machine is capable of cutting materials in various shapes and sizes, making it ideal for industries such as construction, mining, and automotive manufacturing, where different materials are used for different applications.